
Does the wire have multiple cutting functions?
Time:2014-07-22 11:44Reading:time
Have repeatedly cutting wire (wire cutting and working principle of the same), in the process, the control system will be programmed to automatically adjust the machining parameters (the number and speed of the wire tube of the high-frequency pulse width pulse power, and, in the process), but also can artificially change the processing parameters, the proper adjustment.
Basic wire wire cutting in keeping with simple structure and low cost, good effect, use process consumption characteristics, reference international advanced concepts and EDM precision mold processing equipment of multiple cutting technology (i.e. the first cut with large quasi high speed electric gauge rough cutting second times. Third, or even fourth, fifth times cutting, and then use the quasi fine gauge and subtle surface repair regulations will step by step light, to obtain the machined surface quality and machining accuracy is ideal), and the machine hardware upgrade, improve the machine precision and improve the stability of the machine. The machine is more humanized, convenient and wider than the fast wire. So the wire has brought a revolution to the mold industry, greatly improve the quality of the original wire processing weakness, and greatly reduce the mould manufacturing cost! -- wire wire price, wire quality!
What is in WEDM, in WEDM machine (Medium-speed Wire cut Electrical Discharge Machining, abbreviated MS-WEDM) is a reciprocating high speed WEDM machine category, is in high speed reciprocating WEDM machine to realize the multiple cutting functions, known as "in wedm". Go out wire technique here, the so-called "wire" does not mean that the speed of the wire between high speed and low speed, but the composite wire cutting machine, the wire is in principle machining with high speed (8-12m/s) wire, low speed with precision machining (1-3m/s) wire, this work is relatively stable and the jitter is small, and reduce the error caused by repeatedly cutting deformation and molybdenum wire loss, the processing quality is relatively high, the machining quality between high-speed wire machine and low-speed wire machine. Therefore, it can be said that what the users call "walking wire" is actually the reciprocating wire electrical discharge wire cutting machine, which refers to some processing technology of low-speed wire winding machine, and realizes stripless cutting and multiple cutting. In the practice, it is concluded that the first cutting task in multi cutting is mainly the high-speed and stable cutting. The peak current and the longer pulse width can be used for large current cutting to obtain higher cutting speed. Second cutting task is to guarantee the processing precision truing. Medium standard can be selected to make the roughness of Ra after second cutting between 1.4 and 1.7 mu m. In order to achieve the purpose of refinement, usually with low speed wire, wire speed is 1 ~ 3m/s, and the tracking feed speed limit in a certain range, in order to eliminate the reciprocating cutting stripes, machining precision and obtain the required. Third times, fourth or more cutting (currently go wire control software can realize the seven cutting) task is polishing repair available light, the minimum pulse width (the minimum frequency can be up to 1 s) for repair of light, and the peak current as a function of surface quality requirements vary, in fact, is the process of finishing an electrical discharge grinding processing, little volume, does not change the size of the workpiece. The way of wire walking is like second cutting, which uses low speed wire speed limit feed. Take the wire technology in the machining process, multiple cutting deformation processing also need to pay attention to, because the workpiece cutting, with the effect of processing the original internal stress and thermal stress produced by spark discharge, will produce deformation and orientation, without rules, to make the cutting depth, uneven thickness, influence the machining quality and precision. Therefore, we need to reserve different machining allowance according to different materials, so that the workpiece can fully release the internal stress and complete torsion deformation. In the later multiple cutting, we can have enough margin to finish the cutting process, so that the final size of the workpiece can be guaranteed.
Currently on the market in the wire is by three high frequency wire, a long time to maintain accuracy and smoothness, is a very high cost of products. Design and manufacturing engineers are three before walking the manufacturing a bunch of people, so their electric control box is a leading cabinet.
- pre:Without the
- next:JR teaches you to buy a high cost, medium - walk silk - wire
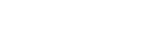