The function and precautions of wire cutting working fluid
Time:2014-07-22 11:29Reading:time
The precondition of steady cutting in WEDM is to ensure continuous wire in the process of cutting. The wire breaking probability increases with the increase of discharge energy and cutting thickness, which is closely related to the ion bombardment, the cooling state and residence time of the electrode wire in the discharge channel.
The efficiency of the cutting and the surface roughness are also related to the cooling and deionization of the poles and the recovery of the insulation. When using a mechanical oil emulsion containing about 5% as the working medium, after cutting on cutting workpiece surface there are two phenomena: the first specimen cutting is finished is adhered to the substrate, the general need to force even knock can make matrix and detachment; secondly after cutting specimen surface covered with adhesive even ablationa powder production, need to clean kerosene.
This is mainly accompanied by the high temperature above 10000 degree C in the discharge channel. The working medium will decompose and generate a large number of polymer compounds and react with metal etch products to form colloidal or granular materials. These substances will adhere to the slit and mainly accumulate at the outlet of the slit, which will seriously affect the removal of the corrosion products and make the fresh working medium entry into the slit very difficult. Because between the poles cannot guarantee the working medium continuously updated, it will directly affect the continuation of normal discharge even in mixed discharge gap large colloid even within the arc discharge is generated, so that the workpiece and electrode wire surface is not timely cooling, the insulation state is not normal, caused by the normal discharge ratio decreased. The cutting speed is reduced, the workpiece surface burns, serious and reversing stripes make processing quality deterioration and damage caused by severe burn of electrode wire, wire. The emulsion as a working medium for cooling in a channel between the improvement, deionization and restore insulation influence both the workpiece, and the higher wire feed speed is slower, the electrode wire stays in the processing area time will be longer, the probability of broken wires will naturally increase.
The decomposition of emulsion into colloid or granular material in discharge channel is a necessary phenomenon. Therefore, using emulsion as working medium will greatly limit the improvement of cutting process index. The direct result of the deterioration of the interpolar cooling state will cause the WEDM-HS to change the processing condition of the filament with a very conservative discharge energy.
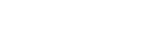